
类别:公司新闻 发布时间:2024-08-29 20:24
8月27日,《科技日报》头版头条专题聚焦铁建重工科技创新: 为中国制造再添一枚金牌 全球最大直径盾构机主大发平台轴承诞生记。全文如下:
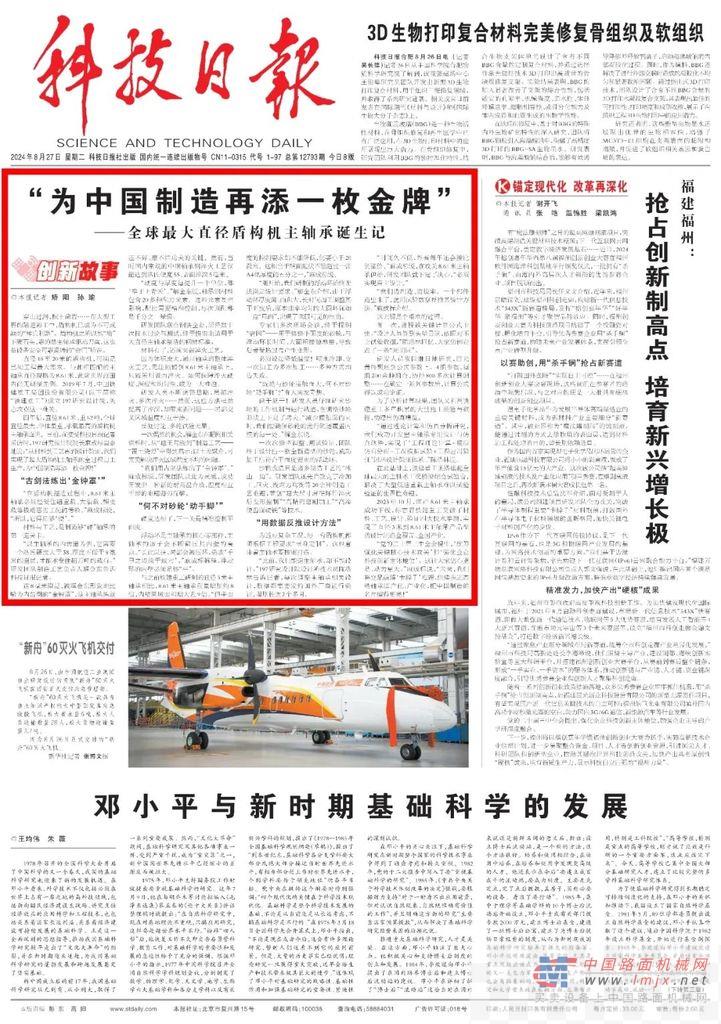
为中国制造再添一枚金牌
全球最大直径盾构机主轴承诞生记
【创新故事】
◎本报记者 矫 阳 孙 瑜
穿山过河,掘土凿岩 在大型工程的隧道施工中,盾构机已成为不可或缺的 神兵利器 。盾构机之所以能 啃 下硬石头,靠的是主轴承驱动刀盘,这也是设备安全可靠运转的 命门 所在。
直径18至20米的盾构机,可满足已知工程最大需求,与此相匹配的主轴承直径规格为8.61米。2019年7月,中国铁建重工集团股份有限公司(以下简称 铁建重工 )成立197研究设计院,矢志攻克这一难关。
四年后,直径8.61米、重62吨,全球直径最大、单体最重、承载最高的盾构机主轴承面世。日前,在接受科技日报记者采访时,197研究设计院院长麻成标自豪地说: 从材料到工艺再到设计验证,我们实现了超大盾构机主轴承的全过程自主生产,为中国制造再添一枚金牌!
古剑法练出 金钟罩
在盾构机掘进过程中,8.61米主轴承必须经受住超重载、大偏载、频变载等极端恶劣工况的考验。 麻成标说, 所以,它得足够 硬 。
材料与工艺,是制造够 硬 轴承的第一道关卡。
以主轴承的内齿圈为例,它需要一个洛氏硬度大于58、厚度不低于8毫米的圈层,才能承受住超万吨的载荷。 研发团队制造工艺负责人解金东告诉科技日报记者。
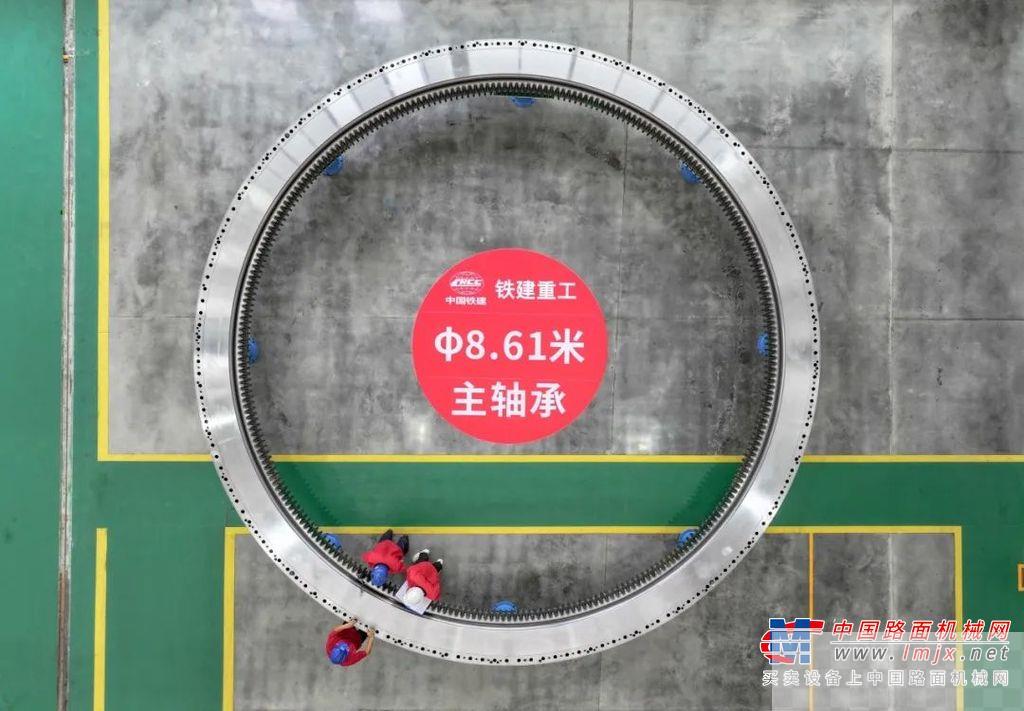
全球最大直径盾构机主轴承
这8毫米圈层,被解金东形象地比喻为内齿圈的 金钟罩 ,是主轴承练就压不碎、磨不烂功夫的关键。然而,当时国内常规的中碳轴承钢淬火工艺仅能达到洛氏硬度55、表面淬深5毫米。
硬度与厚度每提升一个单位,都 难于上青天 。 解金东说,轴承钢材料包含20多种配方元素。这些元素互相影响,配比需要精准控制,每次调配都是千分之一量级。
研发团队联合钢铁企业,历经数十次技术讨论与测试,终于摸索出适用于大直径主轴承制造的钢材标准。
材料有了,还须突破淬火工艺。
因为体积庞大,通用轴承的整体淬火工艺,无法照搬到8.61米主轴承上,只能采用表面淬火。如何保障淬火硬度、深度和均匀性,成为一大难题。
研发人员不断调整思路,局部淬火、多次淬火 然而,这些方法虽然提高了淬深,却带来新问题 局部交叉区域温度相互干涉。
反复讨论、多轮试验无果。
一次偶然的机会,解金东在翻阅相关资料时,从 越王勾践剑 制造工艺 覆土烧刃 中得到启示:以土为媒介,可完美解决淬火区域温度不均的问题。
我们用古剑法练出了 金钟罩 。 麻成标说,研发团队以此为灵感,成功开发出一种新的耐高温介质,温度相互干涉的难题迎刃而解。
何不对砂轮 动手脚
硬度达标了,下一关是精准控制平面度。
浮动环是主轴承的核心零部件,主轴承的滚子会不断碾压其内壁的高点。 长此以往,局部会被压坏,造成 千里之堤溃于蚁穴 。 麻成标解释,浮动环的内壁必须足够 平 。
与之前铁建重工研制的直径3米主轴承相比,8.61米主轴承重量增加约8倍,内壁圆域面积增大近9倍。 但平面度的控制要求却不能降低,仍要小于20微米。这相当于壁面起伏不能超过一张A4纸厚度的五分之一。 麻成标说。
刚开始,我们研制的浮动环始终无法满足设计要求。 解金东介绍,由于浮动环厚度薄、面积大,长时间加工调整其平面度后,原本曲率均匀的大圆环犹如一盘 甩面 ,出现了肉眼可见的扭曲。
专家们多次现场会诊,终于探明 病因 用于修整平面度的砂轮,与浮动环长时间、大面积接触摩擦,导致后者受热过高产生变形。
必须设法降低温度!喷水冷却、变一次加工为多次加工 多种方式均告失败。
既然与砂轮接触面大,何不对砂轮 动手脚 ? 有人突发奇想。
说干就干!研发人员仔细研究砂轮的工作机制与运行轨迹,在调整砂轮形状上下足了功夫。 减少接触面的同时,我们要确保砂轮的运行轨迹覆盖内壁的每一处。 解金东说。
一次次修型调整、测试验证,团队终于设计出一款全新造型的砂轮,成功加工出符合平面度要求的浮动环。
砂轮改造只是诸多制造工艺的 冰山一角 。研发团队还先后攻克了冷加工、回火、残应力均衡等20余种制造工艺难题,首创 超大尺寸薄壁环件淬火后变形控制 高精密磨削加工 高淬硬齿面硬铣 等技术。
用数据反推设计方法
为适应复杂工况,每一台盾构机都须根据工程要求 量身定制 。这也意味着主轴承要按需打造。
此前,我们能造主轴承,却不能设计。 197研究设计院设计所技术员陈浩林告诉记者,每次调整主轴承相关设计,数据都需要发给国外厂商进行验证,周期长达2个多月。
时间久不说,外商每年还会按比例涨价。 麻成标说,在攻关8.61米主轴承伊始,研发团队就下定了决心, 必须实现自主设计。
我们边制造、边摸索。一个部件造出来了,就用试验数据反推其设计方法。 麻成标介绍。
这无疑是个艰难的过程。
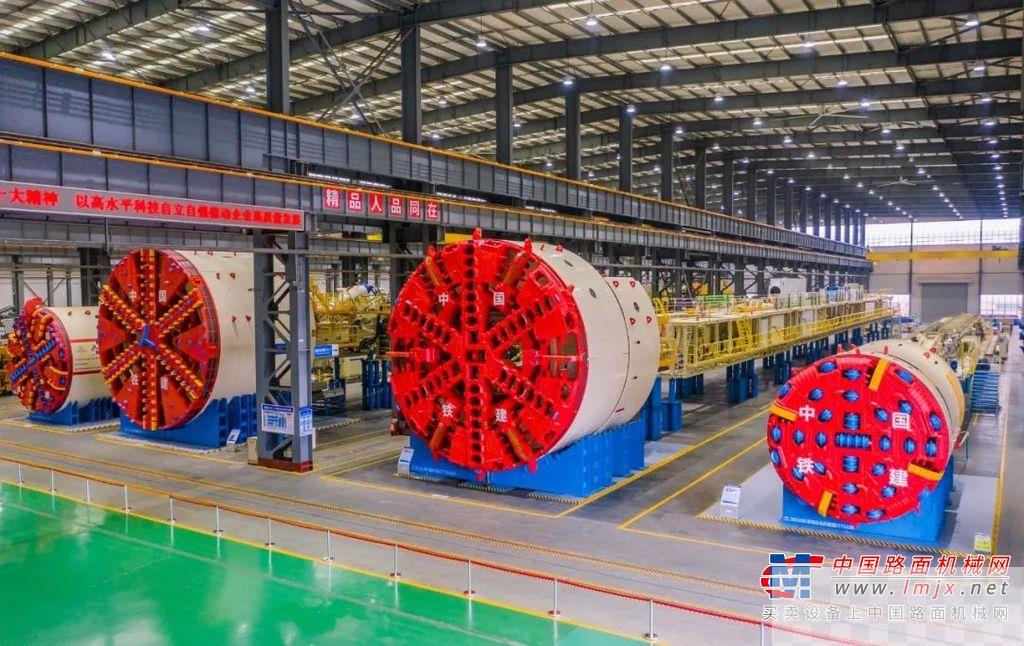
全球最大盾构机生产基地
有一次,进程被关键计算公式卡住。 设计人员算到头晕目眩,依旧对不上试验数据。 陈浩林回忆,大家仿佛走进了一条 死胡同 。
研发人员夜以继日地研究,目光最终聚焦到公式参数上。4组参数,每组200余种组合,历经800多次计算调整 在确定一系列参数后,计算公式得以成功论证。
为了分析计算结果,团队又利用铁建重工多年积累的大量施工经验与数据,构建出仿真模型。
通过理论计算和仿真分析研究,我们成功开发出主轴承专用设计与仿真软件,实现了 工程理论计算+模拟仿真分析+工况模拟试验+工程应用验证 闭环设计验证体系。 陈浩林说。
在此基础上,铁建重工还搭建起全球最大的主轴承工况模拟综合试验台,解决了大型低速重载主轴承难以试验验证的世界性难题。
全球最大直径盾构机主轴承下线现场
2023年10月,国产8.61米主轴承成功下线,标志着铁建重工突破了材料、工艺、设计、验证四大技术难题,实现了直径3米到8.61米主轴承产品型谱设计制造全覆盖、全国产化。
党的二十届三中全会提出, 统筹强化关键核心技术攻关 和 强化企业科技创新主体地位 。这让大家信心更足、动力更大。 麻成标说, 未来,我们将立足破解 卡脖子 难题,继续推进高端轴承国产化、产业化,把中国制造的名片擦得更亮!